Plastic extrusion for bulk custom plastic parts
Plastic extrusion for bulk custom plastic parts
Blog Article
Key Advantages and Factors To Consider of Carrying Out Plastic Extrusion in Your Tasks
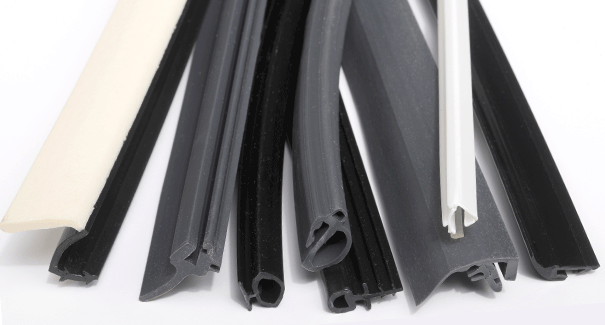
Understanding the Essentials of Plastic Extrusion
Plastic extrusion, a staple in the manufacturing industry, is a process that includes melting raw plastic material and reshaping it right into a constant account. This profile, when cooled down, can be reduced right into desired sizes or coiled for later use. The elegance of plastic extrusion exists in its flexibility. A large range of items, from piping to home window frames, can be produced. The process calls for an extruder, a complex device with a heated barrel, a revolving screw, and a die at the end. The plastic product, in the type of pellets, is fed right into the extruder, where it's melted and compelled with the die, taking its form. The choice of plastic and the layout of the die establish the item's features.

The Economic Benefit of Plastic Extrusion
The financial benefit of plastic extrusion lies mainly in 2 areas: economical material production and useful manufacturing speeds. With plastic extrusion, organizations can create high quantities of material at a lower expense compared to various other techniques. The process flaunts a remarkable production speed, significantly lowering time and additional improving its financial stability.
Economical Product Production
A considerable benefit of plastic extrusion is its impressive cost-effectiveness. Furthermore, the extrusion procedure allows for a high level of precision in forming the plastic, minimizing the need for costly post-production changes or adjustments. All these variables make plastic extrusion a very cost-effective selection for several projects, providing an eye-catching balance in between price and efficiency.
Beneficial Production Speeds
While keeping the cost-effectiveness of the products, another noteworthy benefit of plastic extrusion exists in its fast manufacturing speeds. This combination of high quality, cost-effectiveness, and rate emphasizes the substantial economic advantage of carrying out plastic extrusion in various projects.
Flexibility and Customization: The Toughness of Plastic Extrusion
One of the popular toughness of plastic extrusion depends on its adaptability and customization potential. These qualities unlock to limitless style opportunities, providing makers the ability to tailor items to details demands. This increased degree of customization not just enhances product functionality but additionally substantially enhances product originality.
Unrestricted Layout Possibilities
Plastic extrusion radiates in its capacity to use almost unlimited style possibilities. This method gives liberty to produce intricate profiles and intricate forms, a task hard to attain with other fabrication strategies. Owing to the fluid nature of liquified plastic, the process is versatile enough to yield a varied series of dimensions, dimensions, and forms. The plastic can be adjusted to match special requirements, enabling the manufacturing of customized geometries and conference details customer needs. Plastic extrusion can handle a range of plastic types, increasing its application range. This adaptable method, consequently, offers a variety of industries from building straight from the source and construction to vehicle, product packaging to electronics, and past. With plastic extrusion, the layout possibilities are practically limitless.
Improving Item Originality
The flexibility of plastic extrusion can significantly enhance product originality. This process enables developers to explore different shapes, dimensions, and shades, providing the liberty to produce unique items that stand out out there. It is this personalization that offers an unique identification to each product, distinguishing it from its competitors.
In addition to its aesthetic advantages, the customizability of plastic extrusion also uses useful benefits. Therefore, plastic extrusion not just enhances item individuality yet additionally its energy and bankability.
Layout Limitations in Plastic Extrusion: What You Need to Know
Just how can make restrictions possibly impact the process of plastic extrusion? While plastic extrusion is functional, design limitations can stop its advantages. Certain complicated styles may not be feasible as a result of the restrictions of the extrusion process, possibly limiting the development of complex accounts. The process is less appropriate for multi-chambered or hollow structures. Furthermore, the extrusion process might not always give the wanted surface coating, specifically for those calling for high gloss or optical quality. Material option can likewise posture challenges, as not all polymers are ideal for extrusion. High-temperature resistant you can find out more plastics, for instance, might offer difficulties. Recognizing these restraints is critical for reliable implementation of plastic extrusion in your projects. plastic extrusion.
Reviewing the Ecological Influence of Plastic Extrusion
While understanding layout constraints is a considerable element of plastic extrusion, it is just as essential to consider its environmental effects. The process of plastic extrusion involves melting plastic materials, possibly releasing unsafe gases into the environment. Further, the resulting products are commonly non-biodegradable, adding to land fill waste. Nonetheless, improvements in innovation have permitted more environmentally-friendly techniques. For example, utilizing recycled plastic products in the extrusion procedure can reduce ecological impact. Additionally, establishing biodegradable plastic alternatives can help minimize waste issues. Examining these ecological factors is important when executing plastic extrusion projects, making certain an equilibrium between performance, cost-effectiveness, and environmental responsibility.

Instance Research: Effective Projects Utilizing Plastic Extrusion
Success tales in the area of plastic extrusion abound, demonstrating both the flexibility and performance of this production procedure. plastic extrusion. Another successful instance is the manufacturing of plastic film for product packaging and farming. These circumstances highlight plastic extrusion's crucial function in different fields, confirming to its adaptability, cost-effectiveness, and trustworthy result.
Conclusion
In conclusion, plastic extrusion uses a effective and economical technique for generating complicated shapes with very little waste. Incorporating plastic extrusion right into tasks can lead to successful results, as evidenced by many situation studies.
Plastic extrusion, a staple in the production industry, is a process that includes melting raw plastic material and improving it into a continuous profile. Plastic extrusion can handle a selection go to this web-site of plastic kinds, broadening its application scope.How can develop limitations possibly impact the process of plastic extrusion? The process of plastic extrusion includes melting plastic materials, potentially launching harmful gases into the environment. Using recycled plastic products in the extrusion procedure can lower ecological effect.
Report this page